Fundamental Principles and Process Analysis of Surface Finishing


Surface finishing is a crucial process in manufacturing and material engineering, aimed at improving the physical, chemical, and aesthetic properties of a material's surface. It enhances durability, corrosion resistance, wear resistance, and appearance while also improving adhesion for coatings and reducing friction. Various industries, including automotive, aerospace, electronics, and medical device manufacturing, rely on surface finishing to enhance product performance and longevity.
1. Fundamental Principles of Surface Finishing
Surface finishing is based on several fundamental principles, which define how materials interact with coatings, polishing agents, or chemical treatments:
1.1 Surface Modification
Surface finishing processes alter the surface texture or composition of a material to achieve specific characteristics. This modification can involve:
· Smoothing or roughening the surface to enhance adhesion or reduce friction.
· Adding protective layers to prevent corrosion and wear.
· Modifying surface chemistry to improve electrical conductivity or reduce oxidation.
1.2 Mechanical vs. Chemical Treatment
Surface finishing methods can be broadly classified into:
· Mechanical Processes: Physical methods such as polishing, grinding, and sandblasting that alter surface roughness.
· Chemical and Electrochemical Processes: Techniques like anodizing, passivation, and plating that modify the chemical properties of the surface.
1.3 Surface Energy and Adhesion
The effectiveness of coatings, paints, and adhesives depends on surface energy. A well-finished surface should have optimal surface tension, ensuring that liquids spread evenly and bond effectively.
2. Common Surface Finishing Techniques
Surface finishing techniques vary based on the intended application and material properties. Below are some of the most widely used methods:
2.1 Mechanical Surface Finishing
2.1.1 Polishing
Polishing involves the use of abrasive materials to achieve a smooth and reflective surface. It is commonly used for metals, plastics, and glass to enhance aesthetic appeal and corrosion resistance.
· Methods: Buffing, vibratory finishing, and belt polishing.
· Applications: Jewelry, automotive components, and surgical instruments.
2.1.2 Grinding
Grinding uses abrasive wheels to remove excess material and improve dimensional accuracy. It is typically used for metallic and ceramic parts requiring high precision.
· Methods: Surface grinding, cylindrical grinding, and centerless grinding.
· Applications: Engine components, aerospace parts, and tool manufacturing.
2.1.3 Sandblasting (Abrasive Blasting)
Sandblasting involves the propulsion of abrasive particles against a surface to remove contaminants, rust, or old coatings. This process creates a roughened texture that improves paint adhesion.
· Types of Abrasives: Sand, glass beads, aluminum oxide, and silicon carbide.
· Applications: Cleaning industrial machinery, preparing surfaces for coatings, and etching glass.
2.2 Chemical and Electrochemical Surface Finishing
2.2.1 Electroplating
Electroplating is a process in which a thin metal layer is deposited onto a surface using an electrochemical reaction. It enhances corrosion resistance, wear resistance, and electrical conductivity.
· Common Coatings: Nickel, chromium, gold, silver, and zinc.
· Applications: Automotive parts, electronic components, and decorative items.
2.2.2 Anodizing
Anodizing is an electrochemical oxidation process that creates a durable oxide layer on metals, particularly aluminum. It improves corrosion resistance and color durability.
· Types:
o Type I (Chromic Acid Anodizing) – Thin, protective coating.
o Type II (Sulfuric Acid Anodizing) – Medium thickness, suitable for coloring.
o Type III (Hard Anodizing) – Thick, wear-resistant layer for industrial use.
· Applications: Aerospace components, consumer electronics, and architectural materials.
2.2.3 Passivation
Passivation is a chemical process that removes surface contaminants and enhances the natural corrosion resistance of metals like stainless steel. It is commonly used in medical and food-processing industries.
· Chemicals Used: Nitric acid, citric acid.
· Applications: Medical implants, food processing equipment, and aerospace components.
2.2.4 Chemical Etching
Chemical etching uses acidic or alkaline solutions to remove material selectively, creating fine details and intricate patterns without mechanical stress.
· Applications: Circuit board manufacturing, precision metal parts, and decorative engraving.
2.3 Thermal and Coating-Based Surface Finishing
2.3.1 Powder Coating
Powder coating applies a dry, electrostatically charged powder onto a surface, which is then heated to create a durable, uniform finish.
· Advantages: Scratch resistance, durability, and eco-friendliness.
· Applications: Home appliances, automotive parts, and furniture.
2.3.2 Thermal Spraying
Thermal spraying involves melting a coating material and spraying it onto a surface to enhance wear resistance, heat resistance, and conductivity.
· Types: Flame spraying, plasma spraying, HVOF (High-Velocity Oxy-Fuel) spraying.
· Applications: Aircraft components, turbine blades, and industrial rollers.
2.3.3 PVD (Physical Vapor Deposition)
PVD is a vacuum-based coating process that deposits thin films of metal or ceramics onto surfaces. It is widely used for high-performance coatings in aerospace and tool manufacturing.
· Applications: Cutting tools, watches, optical lenses, and medical instruments.
3. Applications of Surface Finishing in Industries
Different industries utilize surface finishing techniques to enhance performance and aesthetics:
· Automotive: Electroplating, powder coating, and thermal spraying improve durability and corrosion resistance of vehicle parts.
· Aerospace: Anodizing and PVD coatings enhance lightweight durability and wear resistance of aircraft components.
· Electronics: Electroplating and chemical etching enable precision and conductivity in circuit boards and semiconductors.
· Medical Devices: Passivation and PVD coatings ensure biocompatibility and sterility in surgical tools and implants.
Surface finishing is an essential step in manufacturing that enhances material properties, durability, aesthetics, and performance. The choice of finishing technique depends on factors like material type, application requirements, and environmental considerations.
As technology advances, intelligent surface finishing systems incorporating AI, automation, and nanotechnology are expected to revolutionize the industry, ensuring even greater precision, efficiency, and sustainability. Companies looking to improve product performance should invest in high-quality surface finishing solutions to maintain a competitive edge in their industries.
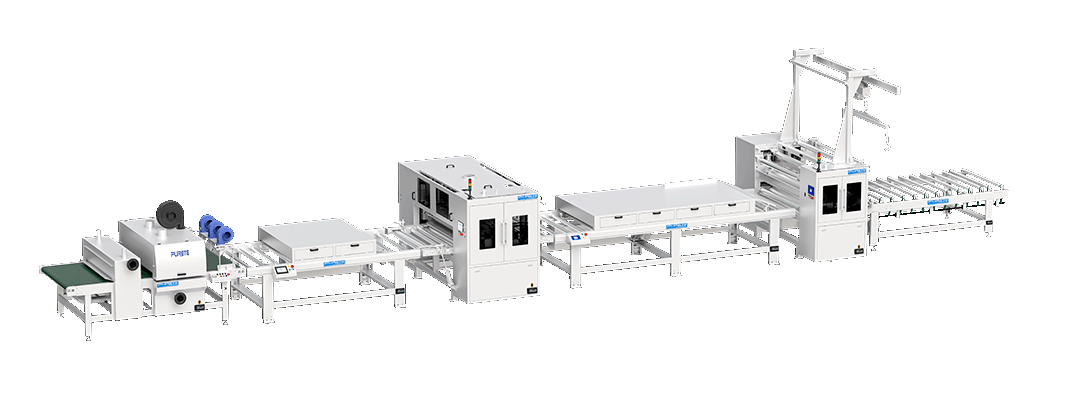
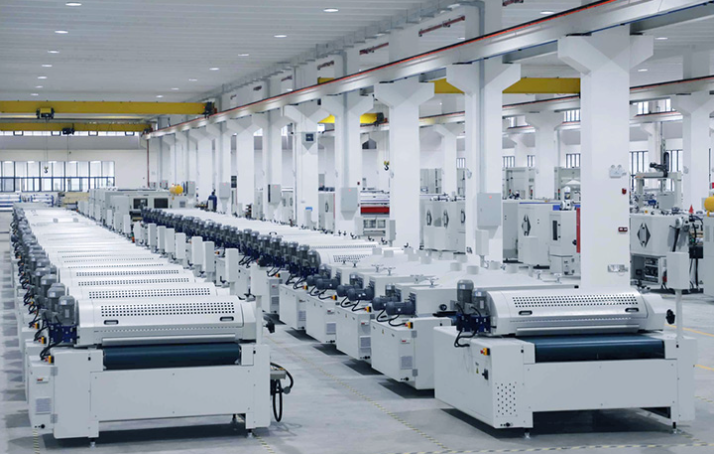
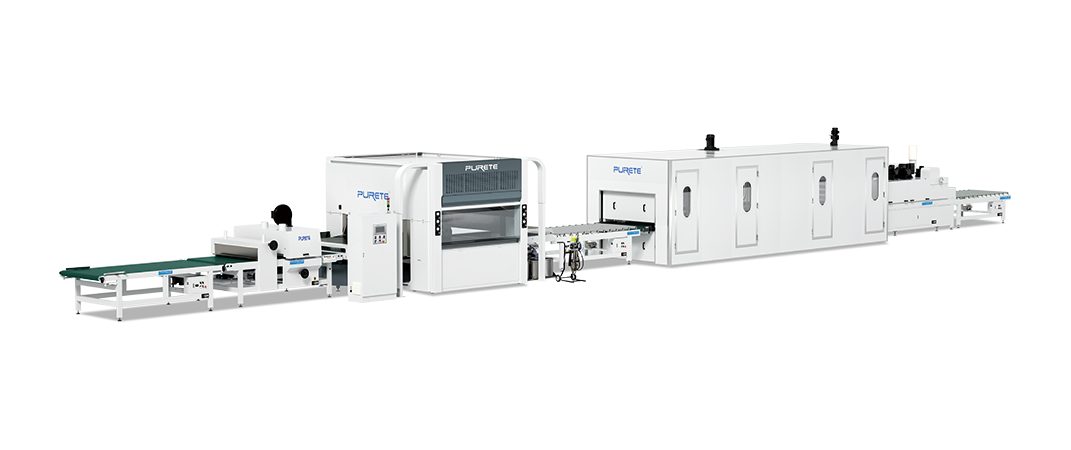
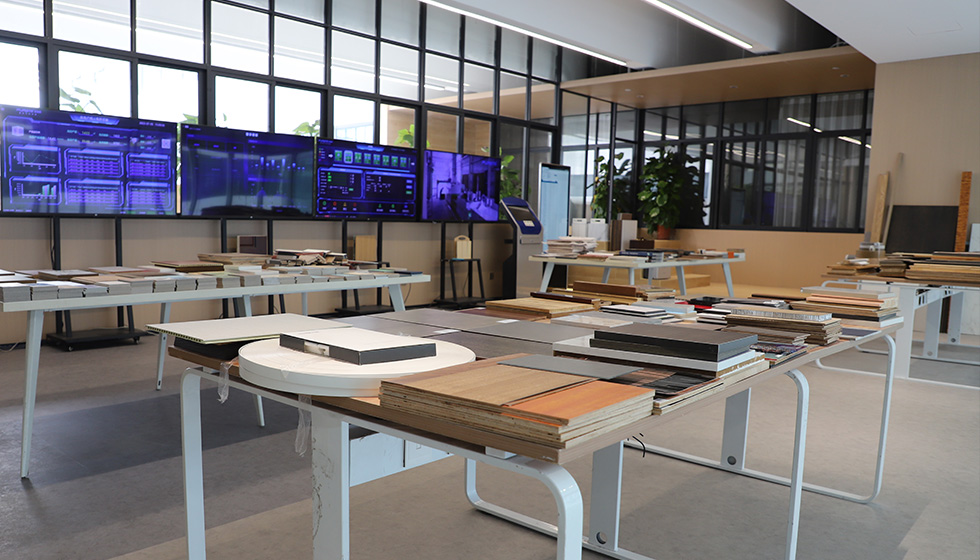
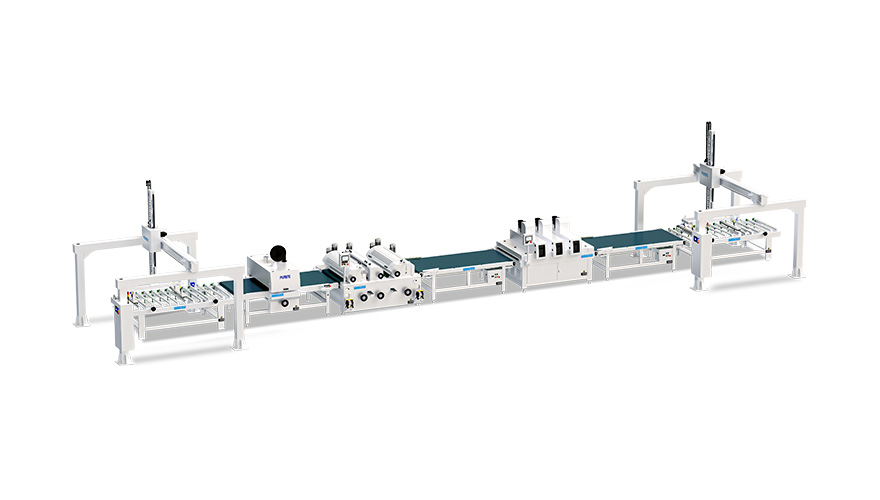


