Comparison Between Intelligent Coating Machine Systems and Traditional Coating Technologies


Coating technologies play a crucial role in various industries, from automotive and aerospace to electronics and furniture. As technology advances, the emergence of Intelligent Coating Machine Systems (ICMS) is revolutionizing the industry, offering enhanced efficiency, precision, and sustainability. Compared to traditional coating methods, intelligent systems integrate automation, artificial intelligence (AI), and smart monitoring, significantly improving performance.
1. Automation and Precision
Traditional Coating Technologies
Traditional coating methods, such as manual spraying, dip coating, and roller coating, heavily rely on human operators. These processes require skilled labor to ensure uniform application, leading to variability in coating thickness and finish quality. Human errors, inconsistencies, and material wastage are common challenges in traditional coating techniques.
Intelligent Coating Machine Systems
ICMS leverages robotic automation, AI algorithms, and sensor-based monitoring to apply coatings with exceptional precision. These systems can automatically adjust spray patterns, coating thickness, and curing parameters based on real-time data. Advanced robotic arms and CNC-controlled spray nozzles ensure uniform application, minimizing defects and reducing material waste.
2. Efficiency and Productivity
Traditional Coating Technologies
Manual and semi-automated coating techniques often result in slower production speeds due to human involvement in setup, application, and quality checks. These methods may require longer drying or curing times, causing delays in production cycles. Additionally, rework due to inconsistencies further reduces efficiency.
Intelligent Coating Machine Systems
ICMS enhances productivity through real-time process optimization. By integrating machine learning algorithms, these systems can self-adjust to optimize material usage, drying time, and production speed. Automated quality control mechanisms detect and correct defects instantly, reducing rework and ensuring higher output rates. Some advanced ICMS setups even feature inline curing systems that speed up drying times, leading to faster product turnaround.
3. Material Utilization and Waste Reduction
Traditional Coating Technologies
Traditional methods often result in excessive material consumption due to overspraying, uneven application, and spillage. For example, in manual spray coating, a significant amount of coating material is lost due to mist dispersion, leading to higher material costs and environmental pollution.
Intelligent Coating Machine Systems
ICMS optimizes material usage through precise control of spray nozzles, adaptive flow rates, and electrostatic coating techniques. These technologies minimize overspray and ensure uniform coating layers, reducing material waste by up to 30-50%. Additionally, smart systems can recycle unused coating material, further enhancing efficiency and sustainability.
4. Environmental Impact
Traditional Coating Technologies
Conventional coating techniques often involve high VOC (volatile organic compounds) emissions, leading to air pollution and environmental concerns. Many traditional coatings require solvent-based formulations, which contribute to hazardous waste and workplace safety risks. Moreover, inefficient material usage increases the carbon footprint of coating processes.
Intelligent Coating Machine Systems
ICMS significantly reduces environmental impact by utilizing low-VOC or water-based coatings, efficient material usage, and advanced filtration systems to capture airborne particles. Some intelligent systems integrate electrostatic or UV-curing technologies, which further reduce solvent emissions and energy consumption. AI-driven process control ensures minimal wastage, making ICMS a more sustainable solution compared to traditional methods.
5. Quality Control and Defect Detection
Traditional Coating Technologies
Quality control in traditional coating methods is often manual and reactive, relying on human inspection after the coating process. This approach can result in missed defects, inconsistent finishes, and increased rework rates.
Intelligent Coating Machine Systems
ICMS integrates real-time defect detection using machine vision, infrared sensors, and AI-based quality analysis. These systems can instantly identify issues such as uneven coating thickness, air bubbles, and surface imperfections, allowing for immediate adjustments. This proactive quality control minimizes product defects and ensures consistent high-quality finishes.
6. Flexibility and Customization
Traditional Coating Technologies
Traditional coating methods require manual adjustments for different materials, shapes, and sizes, making customization time-consuming and labor-intensive. Changing coating parameters often involves trial-and-error testing, leading to inefficiencies.
Intelligent Coating Machine Systems
ICMS offers unmatched flexibility, allowing manufacturers to automatically adjust coating parameters based on product specifications. AI-driven customization enables precise coatings on complex geometries, varying surface textures, and multi-layer applications without manual intervention. Some advanced systems even feature digital twin simulations, enabling operators to test and optimize coatings before applying them in real-world production.
7. Cost Considerations
Traditional Coating Technologies
The initial investment in traditional coating setups is generally lower than intelligent systems. However, higher labor costs, material waste, rework, and quality inconsistencies can lead to increased operational expenses over time.
Intelligent Coating Machine Systems
ICMS requires a higher initial investment due to automation, AI integration, and sensor-based technologies. However, the long-term benefits—including reduced labor costs, lower material waste, increased production efficiency, and consistent quality—lead to significant cost savings over time.
8. Application Industries
Traditional Coating Technologies
Traditional methods are still widely used in small-scale production, low-budget applications, and industries with less stringent quality requirements. Some areas where manual coating remains common include craftsmanship-based industries, furniture manufacturing, and automotive repairs.
Intelligent Coating Machine Systems
ICMS is increasingly adopted in industries that demand high precision, efficiency, and environmental sustainability, such as:
· Automotive: Precision coatings for vehicle components, reducing defects and material waste.
· Aerospace: High-performance coatings on aircraft surfaces to enhance durability.
· Electronics: Thin-film coatings for circuit boards and sensitive electronic components.
· Medical Devices: Biocompatible coatings for implants and surgical tools with extreme accuracy.
· Industrial Equipment: Corrosion-resistant coatings for machinery and heavy-duty applications.
The evolution of Intelligent Coating Machine Systems marks a significant leap forward in coating technology. Compared to traditional coating methods, ICMS provides higher efficiency, precision, material savings, environmental benefits, and cost-effectiveness. While traditional techniques may still be relevant for certain small-scale applications, industries that demand high-quality, consistent, and sustainable coatings are increasingly shifting towards intelligent solutions.
As automation, AI, and smart monitoring continue to advance, ICMS is set to become the standard for modern manufacturing, redefining coating applications across industries. Companies looking to enhance their production capabilities and sustainability efforts should consider investing in intelligent coating technologies for long-term benefits and competitive advantages.
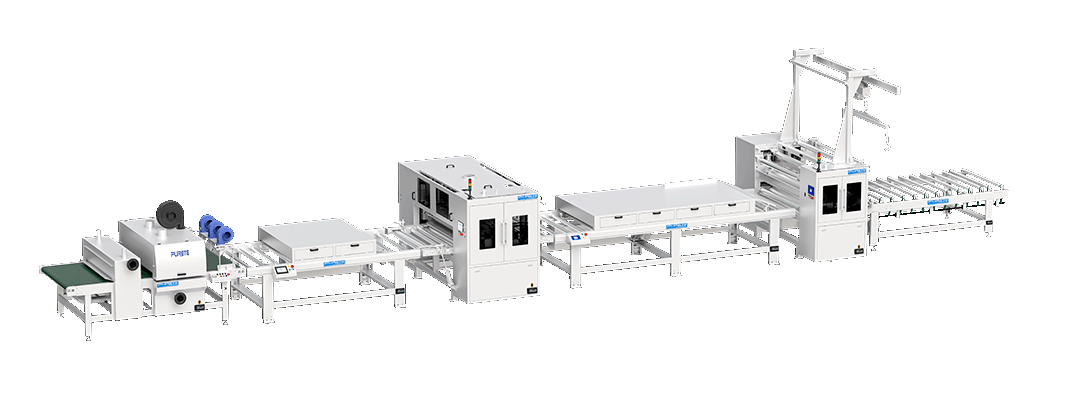
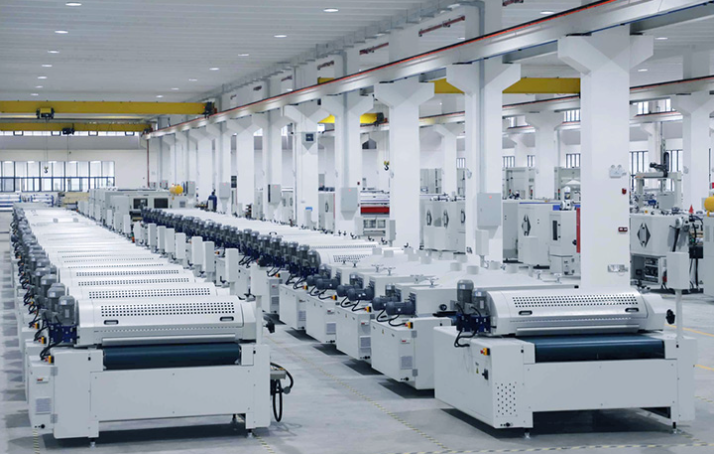
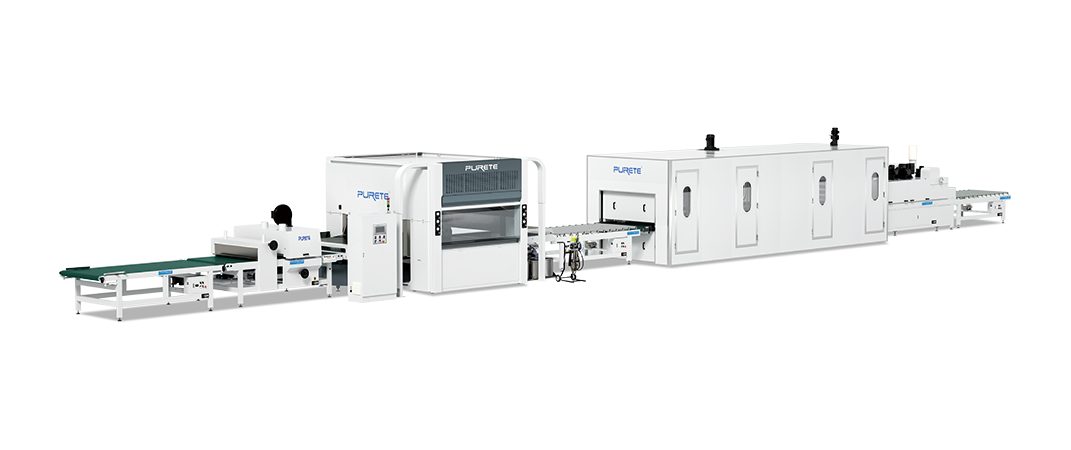
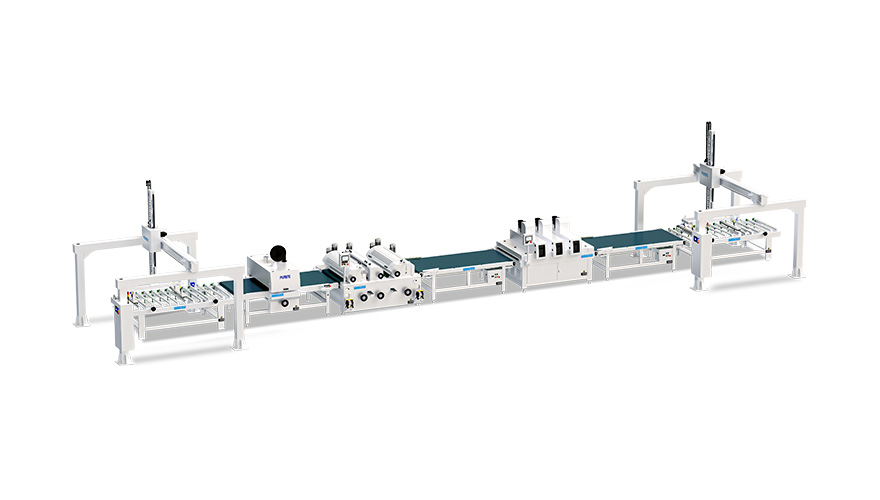
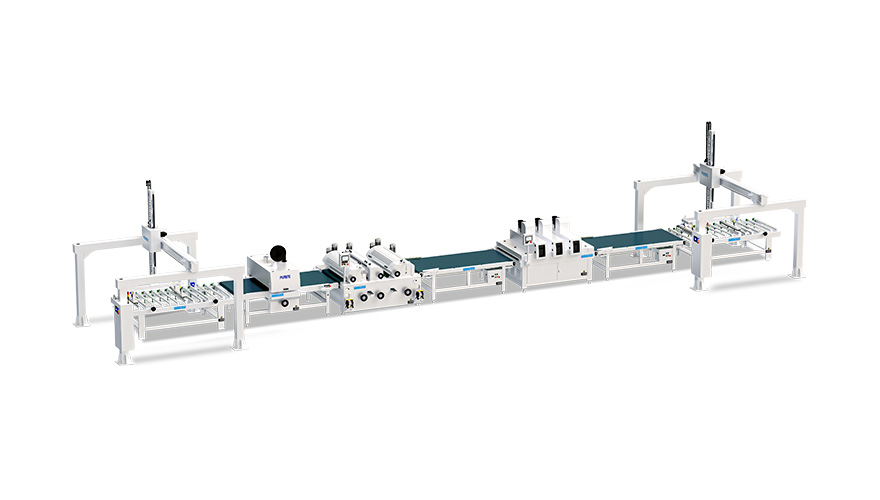


