How Does the PUR Laminating Machine Process Differ from Other Laminating Methods?


Laminating is a crucial process in various industries, used to enhance the durability, appearance, and functionality of materials. Among the different laminating methods available, Polyurethane Reactive (PUR) laminating machines stand out due to their superior bonding strength, flexibility, and resistance to moisture and temperature fluctuations.
1. Understanding PUR Laminating Technology
PUR laminating machines utilize polyurethane-based adhesives that cure through a reaction with ambient moisture. Once applied, the adhesive undergoes a chemical crosslinking process, forming an extremely strong and flexible bond. Key characteristics of PUR lamination include:
Strong Adhesion: Bonds effectively to various substrates, including plastics, wood, metal, textiles, and paper.
Moisture Resistance: Highly resistant to humidity and water exposure, making it ideal for demanding environments.
Flexibility: Maintains elasticity even in extreme temperature conditions, preventing cracking or peeling.
Durability: Long-lasting adhesion compared to traditional laminating methods.
2. Comparison with Other Laminating Methods
2.1. Hot Melt Lamination
Hot melt lamination uses thermoplastic adhesives that are heated until they become liquid and then applied to the substrate. This method is widely used in packaging, textiles, and furniture industries.
Differences from PUR Lamination:
Adhesive Composition: Hot melt adhesives are thermoplastic, meaning they can be reactivated with heat, whereas PUR adhesives chemically cure and cannot be reversed.
Bond Strength: PUR adhesives offer stronger and more durable bonds, especially in environments with fluctuating temperatures or moisture exposure.
Heat Resistance: Hot melt adhesives soften under high temperatures, whereas PUR adhesives remain stable.
2.2. Solvent-Based Lamination
Solvent-based laminating involves dissolving adhesives in solvents, which evaporate during the curing process to create a strong bond. It is commonly used in flexible packaging, labels, and high-performance industrial applications.
Differences from PUR Lamination:
Environmental Impact: Solvent-based lamination releases volatile organic compounds (VOCs), while PUR lamination is more eco-friendly with lower emissions.
Drying Time: Solvent-based adhesives require time for solvent evaporation, whereas PUR adhesives cure faster through moisture reaction.
Chemical Resistance: PUR adhesives provide better resistance to environmental factors such as chemicals, humidity, and extreme temperatures.
2.3. Water-Based Lamination
Water-based lamination uses adhesives that are dispersed in water. As the water evaporates, a solid film forms, bonding the laminated layers together. It is frequently used in paper and flexible packaging industries.
Differences from PUR Lamination:
Moisture Sensitivity: Water-based adhesives can be affected by high humidity, while PUR adhesives are highly moisture-resistant.
Bond Strength: PUR adhesives provide stronger bonds, especially for applications requiring long-term durability.
Application Versatility: Water-based adhesives are mainly used for paper and flexible films, whereas PUR adhesives work with a wider range of materials, including rigid surfaces.
2.4. Film Laminating
Film laminating involves applying pre-coated or adhesive-backed films to substrates using heat and pressure. This method is popular for book covers, posters, and printed materials.
Differences from PUR Lamination:
Adhesion Strength: Film lamination relies on surface adhesion, whereas PUR adhesives penetrate the substrate for a more durable bond.
Flexibility: PUR lamination provides a more flexible and impact-resistant finish, whereas film lamination may crack or peel over time.
Application Limitations: Film lamination is typically limited to paper and plastic surfaces, while PUR lamination works on diverse materials.
3. Advantages of PUR Laminating Machines Over Other Methods
Superior Bonding Strength: PUR adhesives form strong molecular bonds, ensuring long-lasting adhesion even under stress.
Moisture and Heat Resistance: Unlike other adhesives, PUR lamination maintains integrity in extreme conditions.
Versatile Material Compatibility: PUR lamination is suitable for wood, textiles, metal, plastic, and composites.
Eco-Friendly Solution: Compared to solvent-based adhesives, PUR adhesives produce minimal VOC emissions.
Flexibility and Durability: Ideal for applications requiring resistance to bending, stretching, and temperature changes.
While various laminating methods exist, PUR laminating machines stand out due to their unmatched strength, flexibility, and resistance to environmental factors. Compared to hot melt, solvent-based, water-based, and film lamination, PUR lamination provides superior performance, making it ideal for industries requiring durable and high-quality adhesion. As industries continue to demand stronger and more sustainable solutions, PUR laminating technology remains a top choice for advanced manufacturing applications.
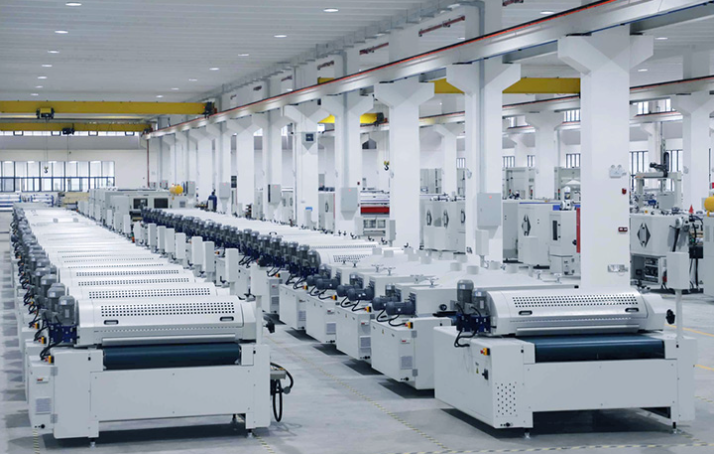
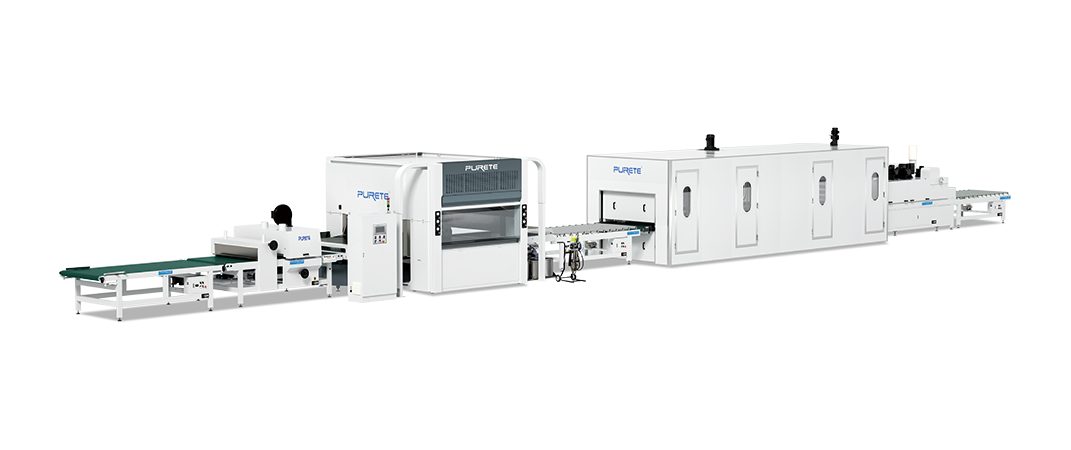
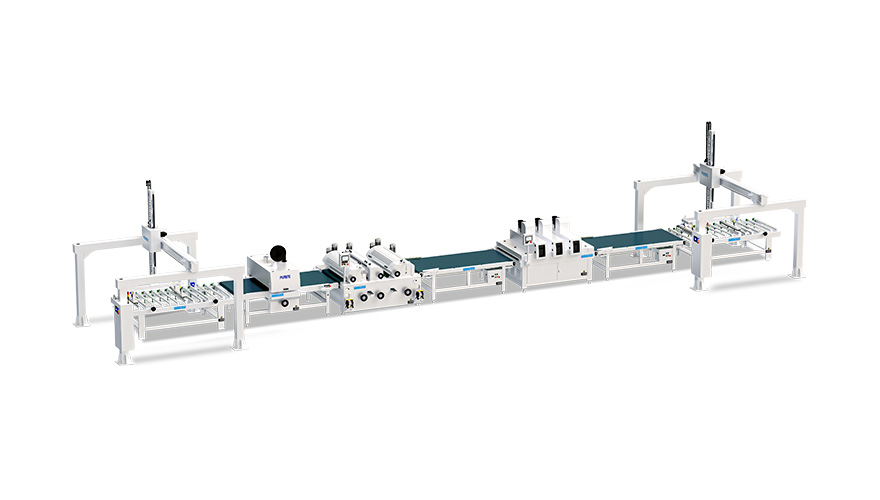
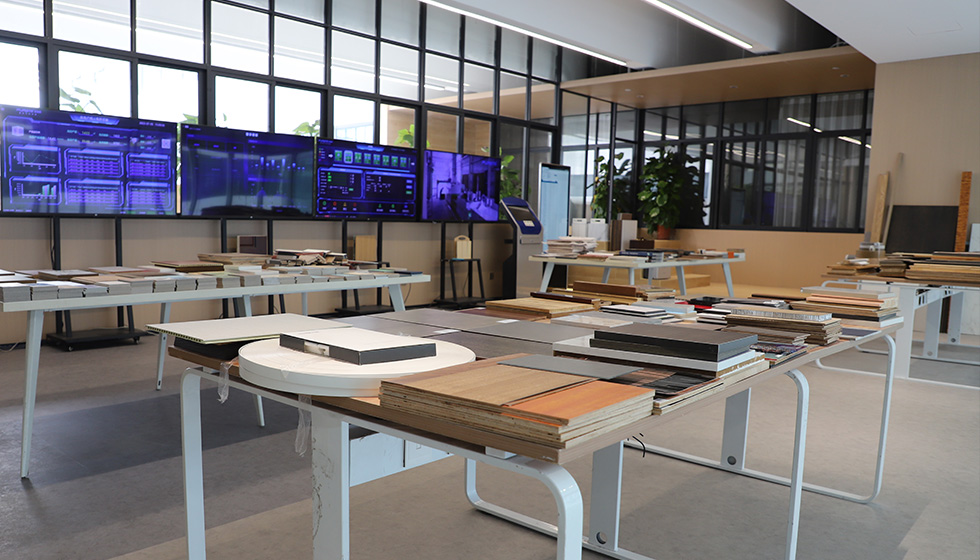
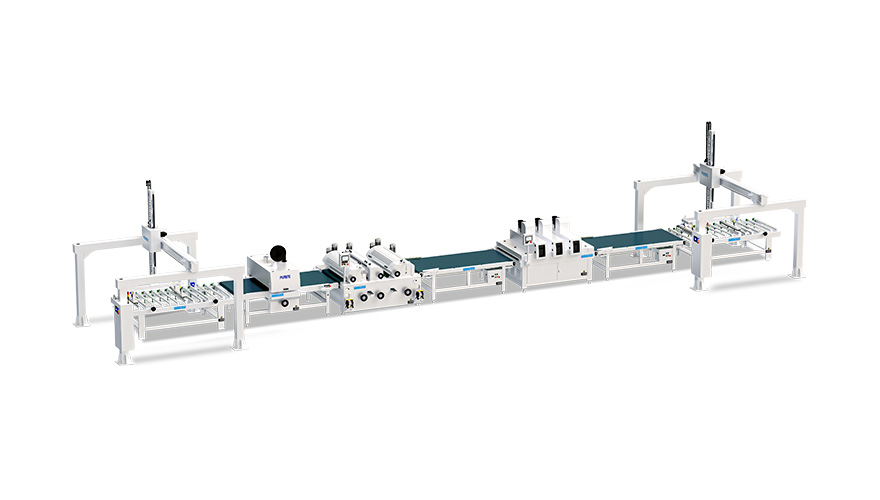


