What Is the Principle of Roller Coating Machine?


In modern industrial manufacturing, surface treatment is essential for enhancing product durability, functionality, and aesthetics. Among the various surface coating technologies available, roller coating stands out for its efficiency, uniformity, and versatility. Roller coating machines are widely used in industries such as furniture, construction materials, packaging, electronics, and automotive manufacturing.
Basic Concept of Roller Coating Machine
A roller coating machine is a specialized device designed to apply a controlled and uniform layer of coating material—such as paint, varnish, adhesives, or other liquids—onto flat or slightly contoured surfaces. As the name suggests, the machine uses rollers to transfer the coating material onto the substrate, ensuring consistent thickness and surface finish.
Roller coating is particularly valued for its ability to handle large volumes of flat products quickly and with minimal material waste, making it highly cost-effective and environmentally friendly.
Core Working Principle of Roller Coating
The fundamental working principle of a roller coating machine revolves around the use of two or more rollers that interact with the coating material and the substrate in a precise and controlled manner. The key elements include:
1. Coating Roller and Application Roller
Coating Roller (Doctor Roller): This roller is in direct contact with the coating material reservoir or tank. It picks up a measured amount of material on its surface.
Application Roller: The coating roller transfers the material to the application roller, which then applies it to the substrate.
Depending on the design, sometimes the coating roller itself directly contacts the substrate. In other designs, an intermediary roller is used to fine-tune the coating thickness before final application.
2. Gap Control
The distance between the rollers, known as the "nip" or "gap," plays a critical role in determining the thickness of the coating applied to the substrate. Adjustable mechanisms allow operators to fine-tune the gap according to the specific requirements of each job.
A smaller gap results in a thinner coating layer.
A larger gap allows for a thicker application.
Some advanced roller coaters use micro-adjustment systems and digital controls to precisely manage this gap, ensuring high accuracy and repeatability.
3. Speed Regulation
Another crucial aspect is the control of roller rotation speed and conveyor speed (if the substrate moves under stationary rollers).
Roller Speed: Faster roller speeds can apply thinner coatings and improve surface smoothness.
Conveyor Speed: The speed at which the substrate passes through the machine must be synchronized with the roller speeds to achieve a uniform coating.
Modern roller coating machines often include variable frequency drives (VFDs) or servo motors to precisely regulate speeds and maintain optimal synchronization.
4. Coating Material Transfer
The coating material is typically fed into the machine either manually or through a pumping system. Excess material on the rollers is controlled using:
Doctor Blades: Thin blades that scrape off surplus material, leaving a consistent layer.
Metering Systems: Devices that regulate the volume of material applied to the roller surface.
This ensures minimal waste and helps maintain uniformity across large production batches.
5. Substrate Handling
Roller coating machines are primarily designed for flat or lightly contoured substrates. The substrate is fed into the machine via a conveyor belt or rollers, passes through the coating section, and exits with a freshly applied layer of coating material.
Proper substrate alignment and tension control are essential to avoid defects like uneven thickness, bubbles, or coating streaks.
6. Drying and Curing
After the coating is applied, the substrate usually moves to a drying or curing section:
Hot Air Dryers: Use heated airflow to evaporate solvents.
Infrared (IR) Dryers: Provide rapid surface drying.
UV Curing Units: Instantly harden UV-curable coatings through ultraviolet light exposure.
Effective drying or curing is critical to ensure the coating achieves its intended hardness, adhesion, and durability.
Types of Roller Coating Machines
There are several types of roller coating machines, each designed for specific materials and applications:
Single Roller Coaters: Use one roller directly contacting the substrate. Suitable for simple applications.
Reverse Roll Coaters: The application roller rotates in the opposite direction of the substrate movement, enabling higher precision and thinner coatings.
Curtain Roll Coaters: Create a "curtain" of coating material before it reaches the roller, useful for very smooth, thick coatings.
Gravure Roll Coaters: Feature engraved rollers that carry precise amounts of coating material, ideal for patterned applications.
Choosing the right type depends on factors like coating material properties, substrate characteristics, desired finish quality, and production volume.
Advantages of Roller Coating Machines
Roller coating technology offers numerous benefits, including:
High Efficiency: Capable of coating large surface areas rapidly.
Material Savings: Minimal overspray and waste compared to spray coating.
Consistency: Uniform thickness and excellent surface finish.
Flexibility: Compatible with a wide range of coating materials and substrates.
Low Maintenance: Simple design allows for easy cleaning and maintenance.
These advantages make roller coating machines an attractive choice for industries demanding high-volume production with consistent quality.
Applications of Roller Coating
Roller coating machines are used in a variety of industries, including:
Furniture Manufacturing: Coating MDF panels, veneers, and laminates.
Flooring Production: Applying finishes to wood, vinyl, or composite flooring.
Automotive Industry: Coating interior panels, dashboards, and trims.
Electronics: Surface coating for device casings and panels.
Construction Materials: Coating metal sheets, composite panels, and insulation boards.
In each of these applications, roller coating delivers high-quality, durable finishes that enhance both the appearance and functionality of the final products.
The principle of the roller coating machine is based on controlled transfer of coating materials through precision-engineered rollers to achieve a consistent, high-quality surface finish. With its efficiency, material savings, and versatility, roller coating technology has become indispensable across multiple industries.
As manufacturing demands continue to evolve, the roller coating machine will remain a key player in ensuring that surfaces are not only protected but also visually appealing and performance-enhanced. Future advancements, such as intelligent automation and eco-friendly coating technologies, promise to make roller coating even more efficient, sustainable, and versatile.
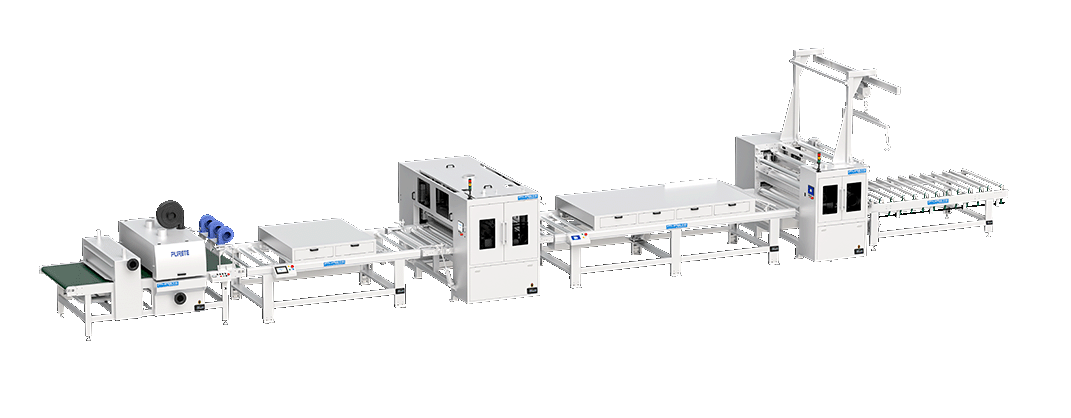
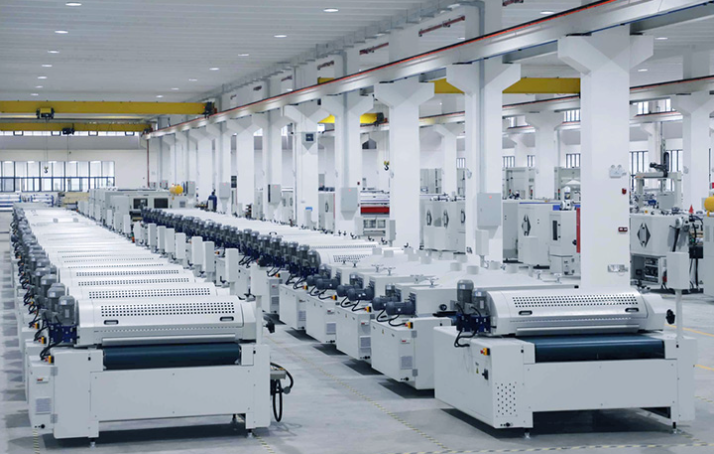

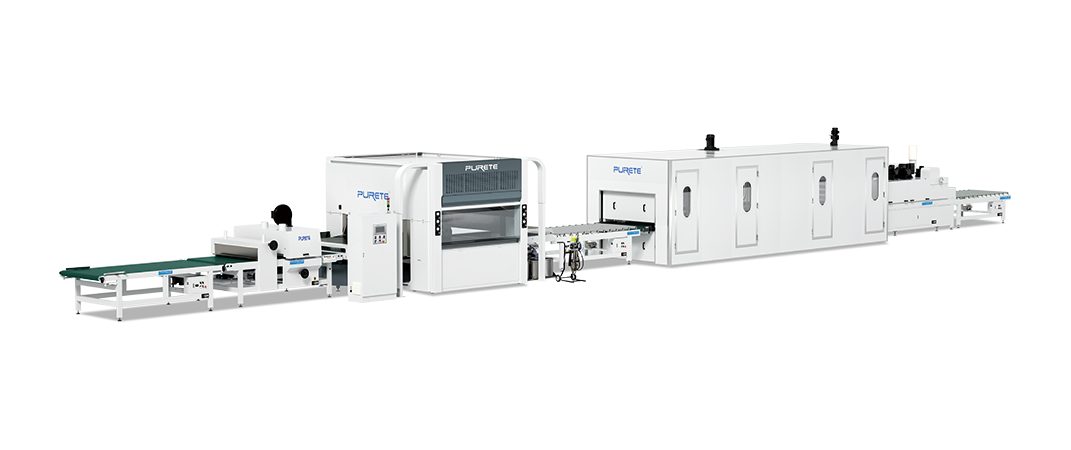

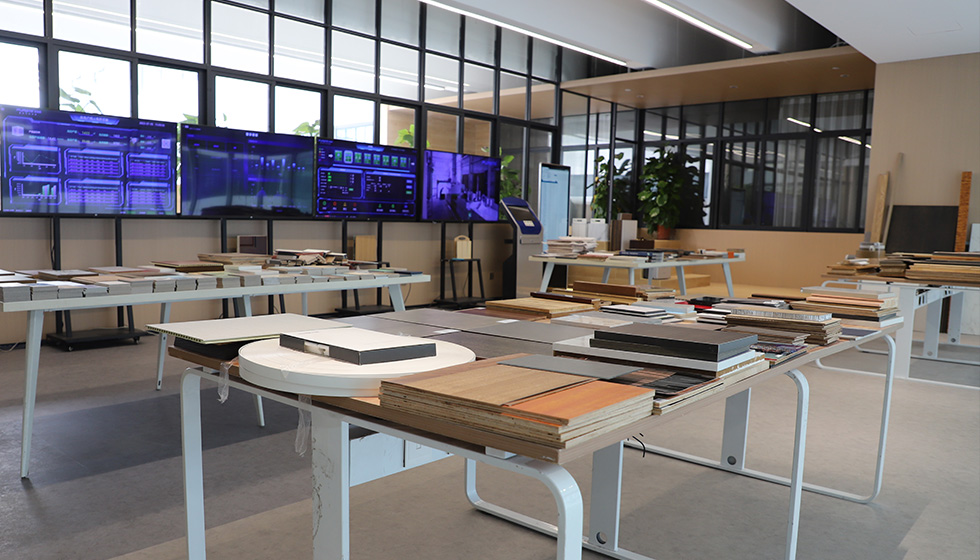
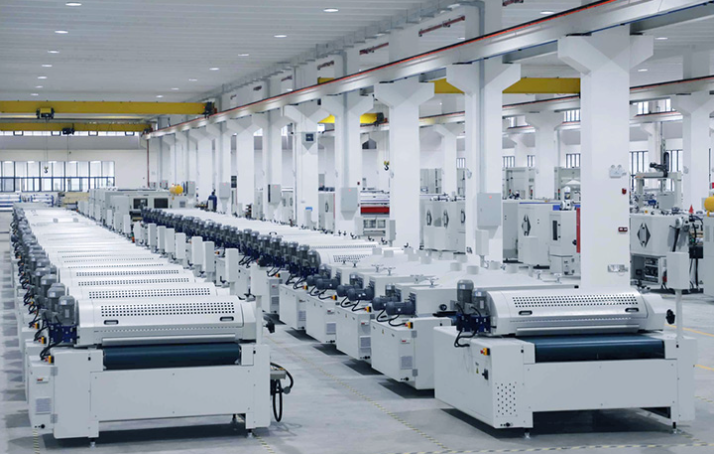
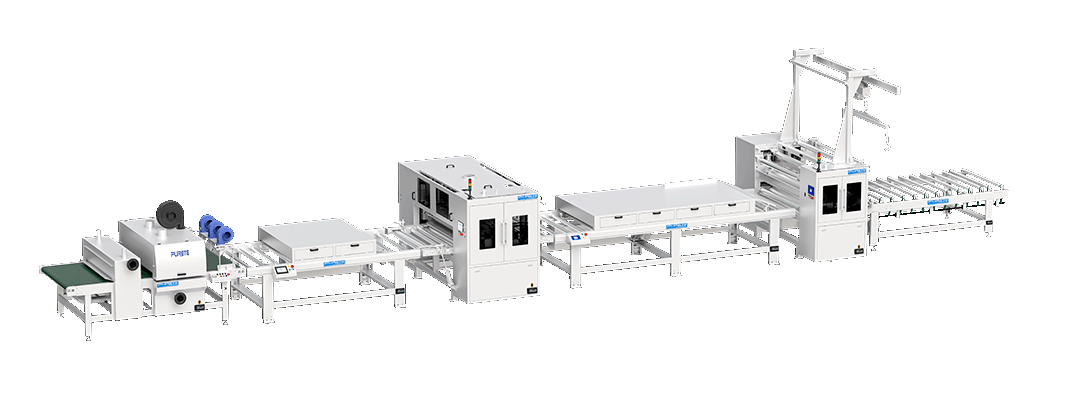