PUR Laminating Production Line: Innovative Adhesion Solutions


The PUR Laminating Production Line represents a cutting-edge solution in adhesive technology, providing superior bonding performance across various industries. By utilizing Polyurethane Reactive (PUR) adhesives, this process ensures stronger, more durable, and aesthetically pleasing laminated products.
Principles and Process of PUR Laminating
The PUR laminating process relies on moisture-reactive polyurethane adhesives, which undergo a chemical reaction with ambient humidity to form a highly resilient bond. The key steps in the PUR laminating production line include:
1. Surface Preparation
Cleaning and pre-treating the substrate to remove dust, oil, and contaminants.
Ensuring optimal surface activation for improved adhesion.
2. Adhesive Application
PUR adhesive is applied in a thin and even layer through a precision coating system.
The application method varies based on the material, including roller coating, spray application, or slot die coating.
3. Lamination and Bonding
The adhesive-coated material is pressed against another substrate using controlled heat and pressure.
PUR adhesive remains in a thermoplastic state initially, allowing repositioning if necessary.
4. Curing and Finalization
The adhesive reacts with moisture to undergo a curing process, converting into a thermoset structure.
Once fully cured, the adhesive becomes highly resistant to heat, chemicals, and mechanical stress.
Enhancing Product Strength and Aesthetic Appeal
The PUR laminating process is widely recognized for its ability to enhance both structural integrity and surface quality. Its advantages include:
1. Superior Bond Strength
PUR adhesives form permanent, high-strength bonds that withstand mechanical stress, making them ideal for automotive, furniture, and construction applications.
The moisture-curing process provides exceptional durability, even in extreme environments.
2. Improved Aesthetic Finish
The process creates seamless, bubble-free lamination, enhancing the visual appeal of products.
It supports various decorative finishes, including wood veneers, high-gloss films, and textured laminates.
3. Versatility Across Materials
Works effectively on plastics, metals, textiles, wood, and composite materials.
Ensures consistent adhesion without material deformation or warping.
Environmental Contributions of PUR Laminating Technology
As sustainability becomes a growing concern in industrial production, PUR laminating technology offers significant environmental advantages:
1. Solvent-Free Adhesion
PUR adhesives are solvent-free, reducing emissions of volatile organic compounds (VOCs).
Helps industries comply with strict environmental regulations and improve workplace safety.
2. Reduced Material Waste
Precise adhesive application minimizes material waste, contributing to efficient resource utilization.
The ability to bond diverse materials reduces reliance on mechanical fasteners, leading to lighter, more sustainable products.
3. Energy Efficiency
The low-temperature curing process requires less energy compared to traditional adhesive systems.
This enhances energy savings and reduces the overall carbon footprint of production lines.
The PUR Laminating Production Line is a game-changer in the world of adhesive technology, offering a high-performance, eco-friendly, and aesthetically superior bonding solution. By utilizing moisture-reactive polyurethane adhesives, this method ensures exceptional bond strength, durability, and versatility across industries. Additionally, its solvent-free formulation and energy-efficient curing process contribute significantly to environmental sustainability.
As industries continue to seek innovative and greener manufacturing processes, the adoption of PUR laminating technology will undoubtedly expand, paving the way for more durable, visually appealing, and sustainable products in the future.
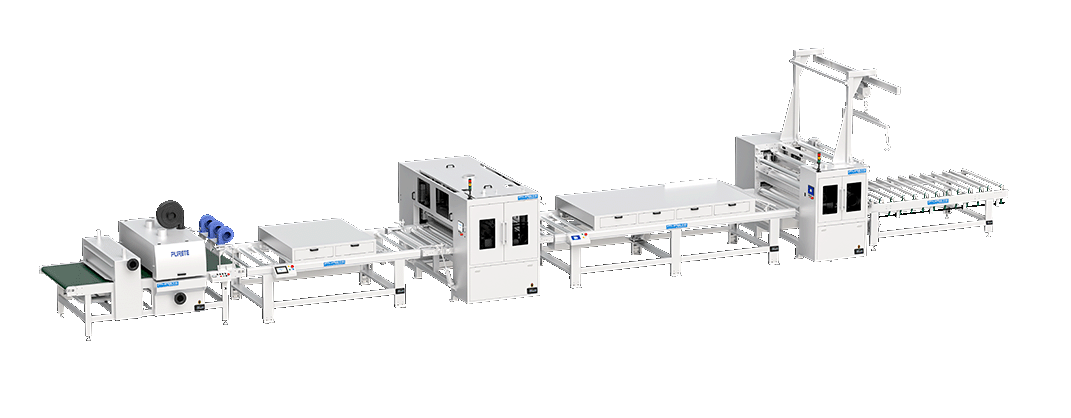
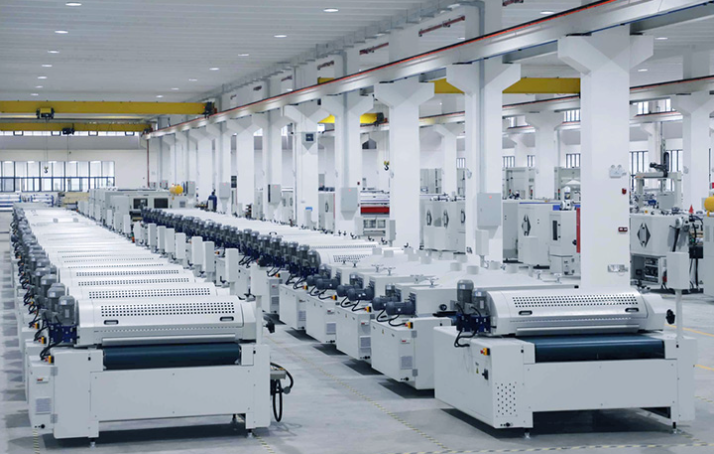

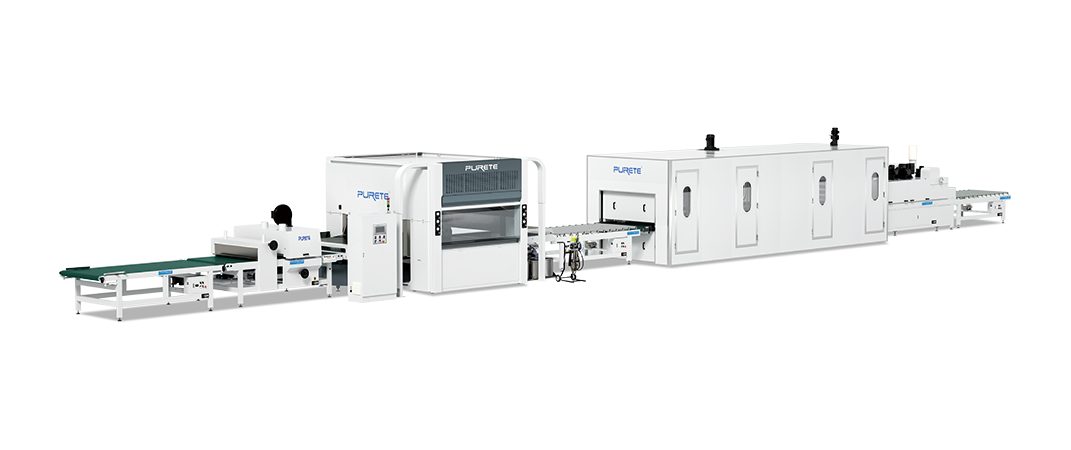

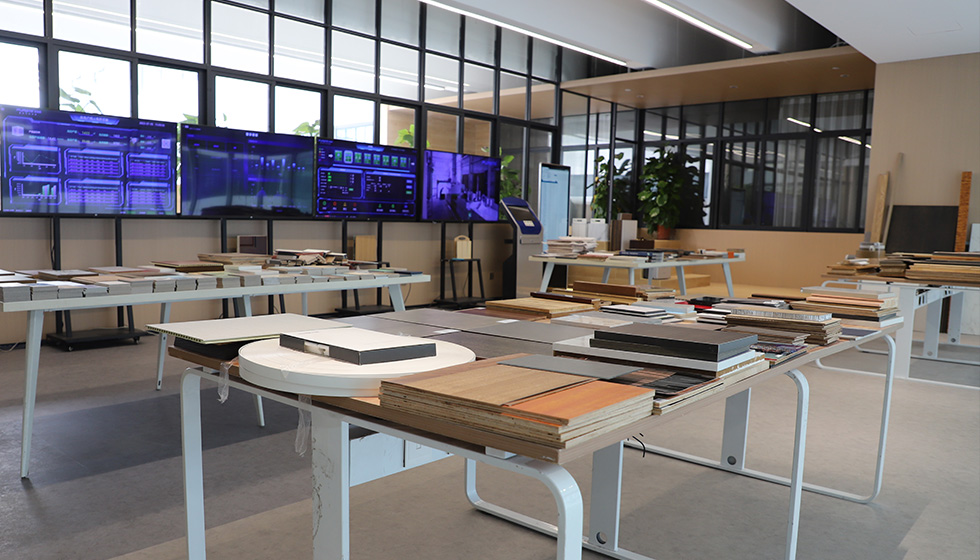
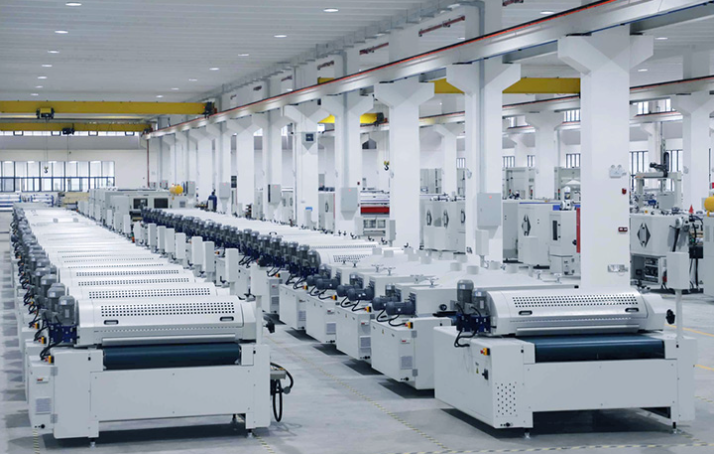
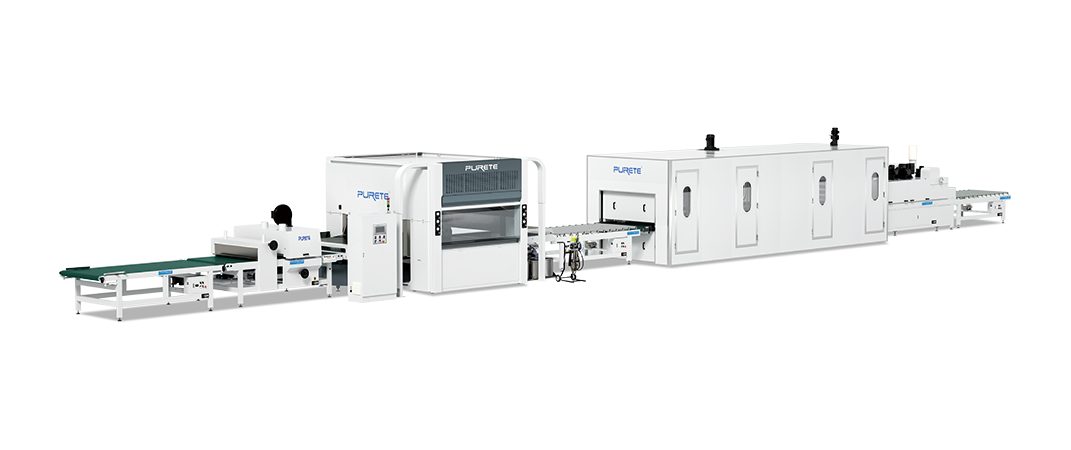