The Widespread Application of Short-Cycle Press Lines in Panel Furniture Manufacturing


In today’s fast-paced furniture industry, efficiency, customization, and quality are more than just goals—they are essential components of staying competitive in global markets. One of the key technologies driving this transformation is the short-cycle press line, which has become a cornerstone in the production of panel furniture. Whether for office desks, kitchen cabinets, wardrobes, or TV stands, the short-cycle press line is now widely adopted for its unmatched speed, precision, and cost-efficiency.
What is a Short-Cycle Press Line?
A short-cycle press line is a specialized industrial system used for laminating decorative surfaces—such as melamine-impregnated paper—onto wood-based panels like particle board (PB), medium-density fiberboard (MDF), and high-density fiberboard (HDF). The process involves applying high pressure and temperature for a short duration—typically 10 to 30 seconds—to permanently bond the decorative layer to the substrate.
Modern short-cycle press lines are integrated systems, often including:
Automatic feeding and stacking systems,
Preheating units,
High-precision hydraulic presses,
Embossing capabilities,
Cooling sections and quality control modules.
1. Supporting Mass Production in Panel Furniture
The primary appeal of short-cycle press lines lies in their exceptional productivity. In furniture factories operating at large scale, these systems enable the lamination of thousands of panels per day with minimal labor and high consistency.
Applications include:
Kitchen cabinets with heat- and moisture-resistant surfaces,
Wardrobes and closets with elegant wood grain textures,
Office desks and partitions with durable and scratch-resistant coatings,
TV cabinets and bookshelves in high-gloss or matte finishes.
By dramatically reducing the pressing cycle, manufacturers can meet tight delivery schedules while maintaining high throughput.
2. Enabling Aesthetic and Functional Versatility
Short-cycle press lines are highly compatible with a wide variety of design papers, foils, and overlays, enabling furniture makers to offer rich customization options. With growing demand for design-oriented interiors, this versatility is key.
Design options supported by short-cycle press lines:
Wood grain and stone-effect textures,
Matte, gloss, or super-matte finishes,
Embossed-in-register (EIR) surfaces that mimic real wood,
Colored or patterned papers for modern or minimalist styles.
Furniture companies can thus easily switch between different panel designs to cater to regional tastes or brand requirements—without changing the base production setup.
3. Elevating Surface Quality and Product Durability
In panel furniture, surface quality is critical—not only for aesthetic value but also for usability. Short-cycle pressing ensures uniform lamination, free of air bubbles or wrinkles, with strong bonding between the paper and board.
Benefits to final products:
Resistance to scratches, heat, and stains, ideal for kitchens and work surfaces,
Moisture resistance for bathroom furniture or humid environments,
Smooth, easy-to-clean surfaces for low-maintenance use.
By achieving precise control of pressure and temperature, the press line enhances both the look and performance of laminated panels, ensuring long-lasting furniture.
4. Improving Production Efficiency and Reducing Costs
Short-cycle press lines are built for automation and scalability, making them ideal for lean manufacturing operations.
Operational advantages include:
Automatic feeding, loading, and unloading systems reduce manual labor,
Minimal material waste through precision cutting and feeding,
Lower energy consumption per panel compared to traditional hot press methods,
Reduced downtime due to faster cycle times and integrated control systems.
These efficiencies translate into lower production costs, allowing furniture makers to price competitively or invest in higher-margin design features.
5. Meeting the Needs of Customized and Small-Batch Production
Although traditionally used for high-volume production, modern short-cycle press lines can also be configured for flexible manufacturing. This includes smaller batch sizes, quick design changes, and short lead times—all of which are increasingly in demand in the era of personalized furniture.
Digital control systems allow operators to adjust settings for different paper types, board thicknesses, and textures, enabling on-demand production for retailers, contractors, and online furniture brands.
6. Supporting Green and Sustainable Manufacturing
Sustainability is now a core priority in furniture manufacturing, and short-cycle press lines contribute positively in several ways:
Energy-efficient pressing cycles reduce carbon footprint,
Low emissions when used with eco-friendly adhesives and laminates,
Waste minimization through precise control and automation,
Compatibility with recycled or eco-certified board materials.
Many manufacturers are now combining short-cycle technology with renewable energy sources and closed-loop water or heating systems to build greener production lines.
Conclusion: A Cornerstone of Modern Furniture Manufacturing
As the demand for stylish, functional, and affordable panel furniture continues to grow, short-cycle press lines have become a foundational technology for manufacturers worldwide. Their ability to laminate quickly, uniformly, and cost-effectively makes them ideal for large-scale production, while their design flexibility and energy efficiency support modern market needs and sustainability goals.
From kitchen cabinets to contemporary wardrobes and minimalist office sets, short-cycle pressing empowers the industry to deliver high-quality furniture that aligns with consumer trends—fast, efficiently, and with lasting appeal.
For furniture manufacturers aiming to scale operations, expand design options, or reduce their environmental impact, the short-cycle press line is more than an investment—it's a strategic advantage.
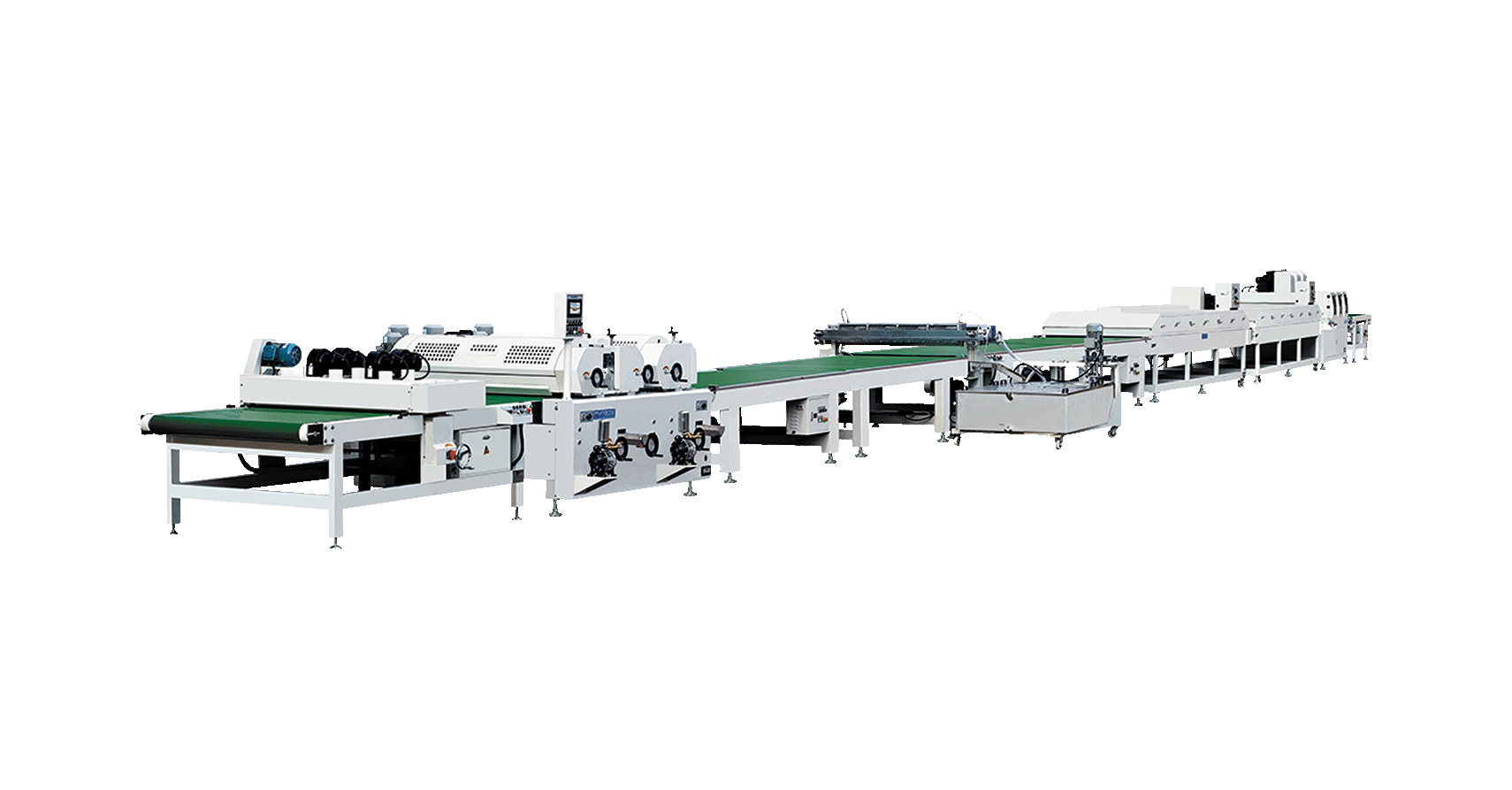


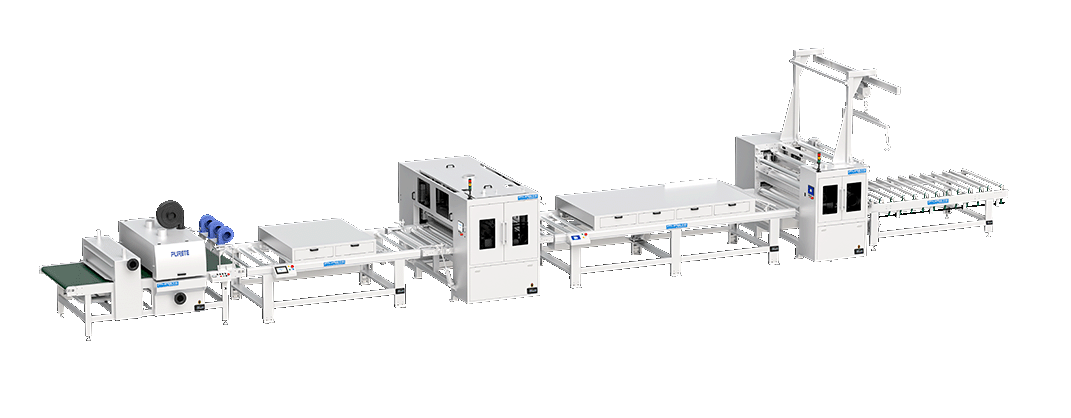
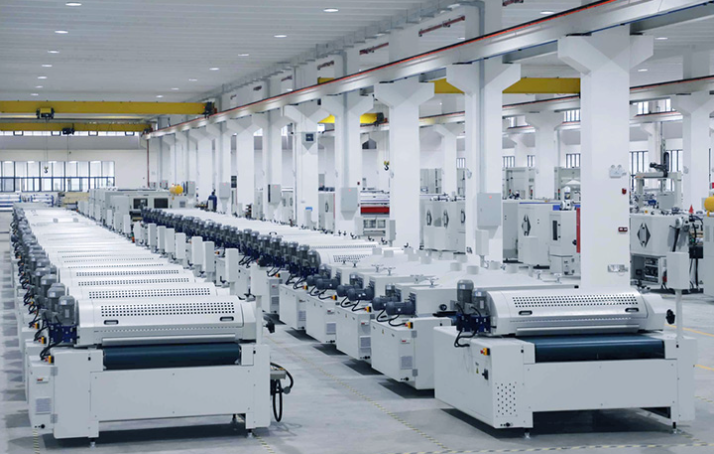
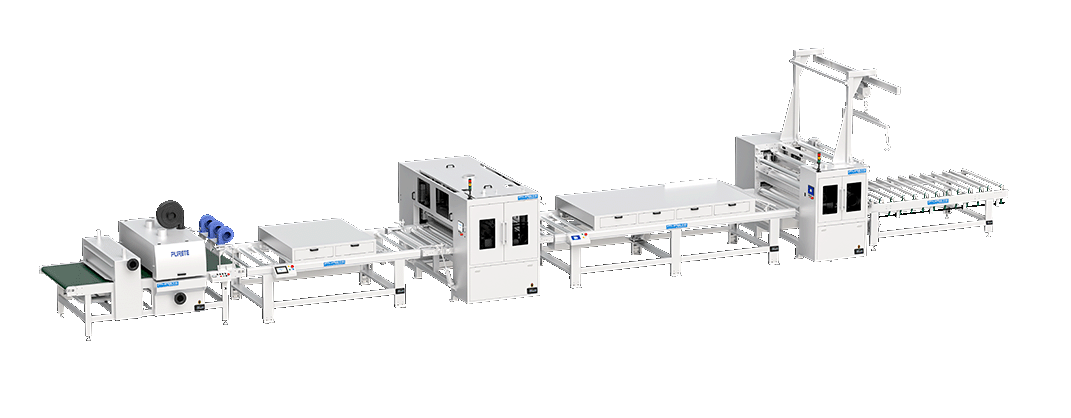
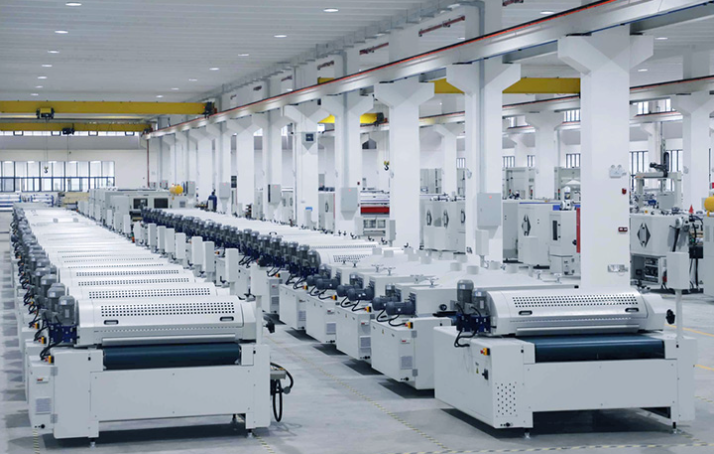
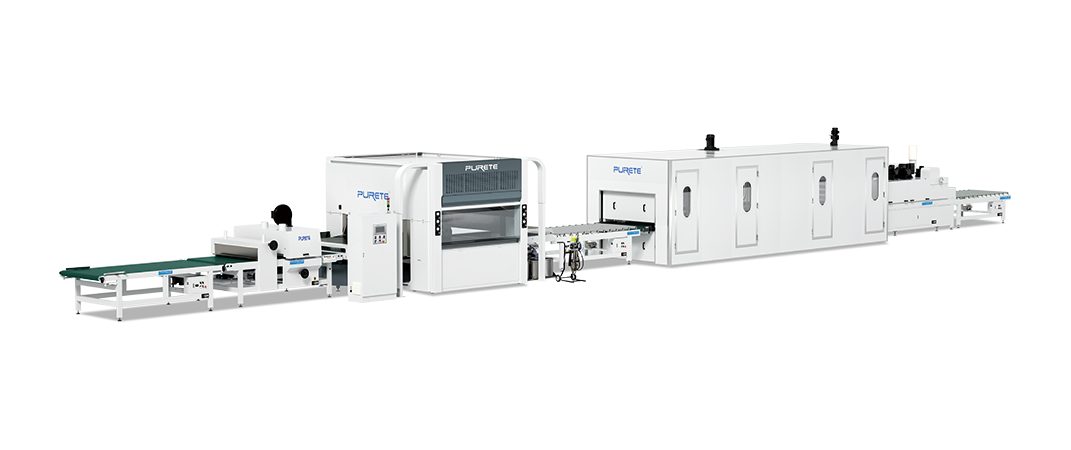