Spray Painting Machine: Types and Technologies for Modern Furniture Finishing


In today’s competitive furniture manufacturing industry, surface finishing is more than just a final step—it is a critical process that affects both aesthetic appeal and product durability. The choice of spray painting equipment plays a vital role in achieving high-quality finishes, operational efficiency, and cost control. From simple panel doors to intricately designed cabinets, different spray painting technologies are available to suit a variety of application needs.
1. Reciprocating Spray Painting Machine: Ideal for Flat Surfaces
Reciprocating spray machines are specifically designed for repetitive back-and-forth motion during painting. This makes them highly suitable for flat panel surfaces such as wooden doors, tabletops, or other furniture components with uniform geometry. The machine typically consists of a conveyor belt that transports the workpieces under a linear spray gun that moves in a reciprocating pattern.
Advantages:
Excellent for high-volume production of flat pieces.
Consistent spray patterns ensure uniform coating thickness.
Easy integration into automated conveyor systems.
Applications:
Interior doors, cabinet panels, drawer fronts, and other flat wood products.
Because of their specialization, reciprocating machines are often the first choice in mass production settings where speed and surface uniformity are key.
2. Robotic Spray Painting: Flexible and Precise for Complex Shapes
As furniture designs become more intricate, manufacturers require painting systems that can handle curved surfaces, carved details, and complex geometries. Robotic spray painting systems meet this challenge with multi-axis arms that provide maximum flexibility in spray angles and movement.
Advantages:
High flexibility for complex 3D objects.
Can be programmed for various shapes and sizes, reducing changeover time.
Improved worker safety by reducing human exposure to chemicals.
Applications:
Custom furniture, ornate cabinets, ergonomic chairs, and items with contours or multiple angles.
Robotic systems are ideal for manufacturers aiming to achieve high customization, consistency, and long-term cost efficiency. The initial investment may be high, but the reduction in labor costs and paint waste justifies the expense over time.
3. Electrostatic Spray Coating: Efficient and Economical
Electrostatic spray machines use electrically charged particles to attract paint to the surface of the workpiece. This method significantly reduces overspray and ensures better paint adhesion, making it one of the most efficient painting technologies available.
Advantages:
Saves paint by reducing overspray and bounce-back.
Creates an even, high-quality finish with minimal material usage.
Suitable for conductive materials like metal or surfaces treated for conductivity.
Applications:
High-end furniture, metal-framed pieces, and office furniture requiring smooth finishes.
Electrostatic spray systems are especially effective in achieving uniform finishes on contoured surfaces while minimizing material waste—making them a go-to option for manufacturers focused on sustainability and cost-efficiency.
4. UV Coating Equipment: Speed and Performance in One Package
UV coating technology has gained popularity in modern finishing lines due to its rapid curing capabilities. UV-curable coatings are applied to the workpiece and immediately exposed to ultraviolet light, resulting in an instant hardening process. This dramatically shortens production cycles and enhances surface durability.
Advantages:
Fast curing—reduces processing time and increases production throughput.
Produces durable, scratch-resistant finishes.
Environmentally friendly due to reduced solvent emissions.
Applications:
Kitchen cabinets, vanity units, flooring panels, and components requiring a hard, glossy, or matte finish.
UV coating systems are essential in high-speed production environments where quality and efficiency must go hand in hand. They're particularly favored in automated painting lines integrated with drying tunnels and material handling systems.
How to Choose the Right Spray Painting Machine?
The decision to choose a particular spray painting system depends on several factors:
Product Type: Flat or 3D, wood or metal, small batch or mass production.
Finish Requirements: High-gloss, matte, scratch-resistant, or eco-friendly coatings.
Production Volume: High-speed lines may benefit from UV curing, while custom work favors robotic systems.
Budget Constraints: Reciprocators and electrostatic systems offer cost-effective solutions for specific applications, while robotic arms and UV systems may require higher initial investment.
Conclusion
As furniture manufacturers strive to meet increasing demands for quality, efficiency, and sustainability, the right spray painting machine can be a game-changer. Whether it's the precision of robotic arms, the speed of UV curing, the economy of electrostatic spraying, or the reliability of reciprocating machines, each technology serves a unique purpose.
By carefully evaluating production requirements and finish standards, businesses can select a spray painting system that not only enhances product quality but also optimizes operational performance. As automation and smart manufacturing continue to evolve, integrating advanced spray painting equipment will become an essential strategy for staying competitive in the global furniture market.
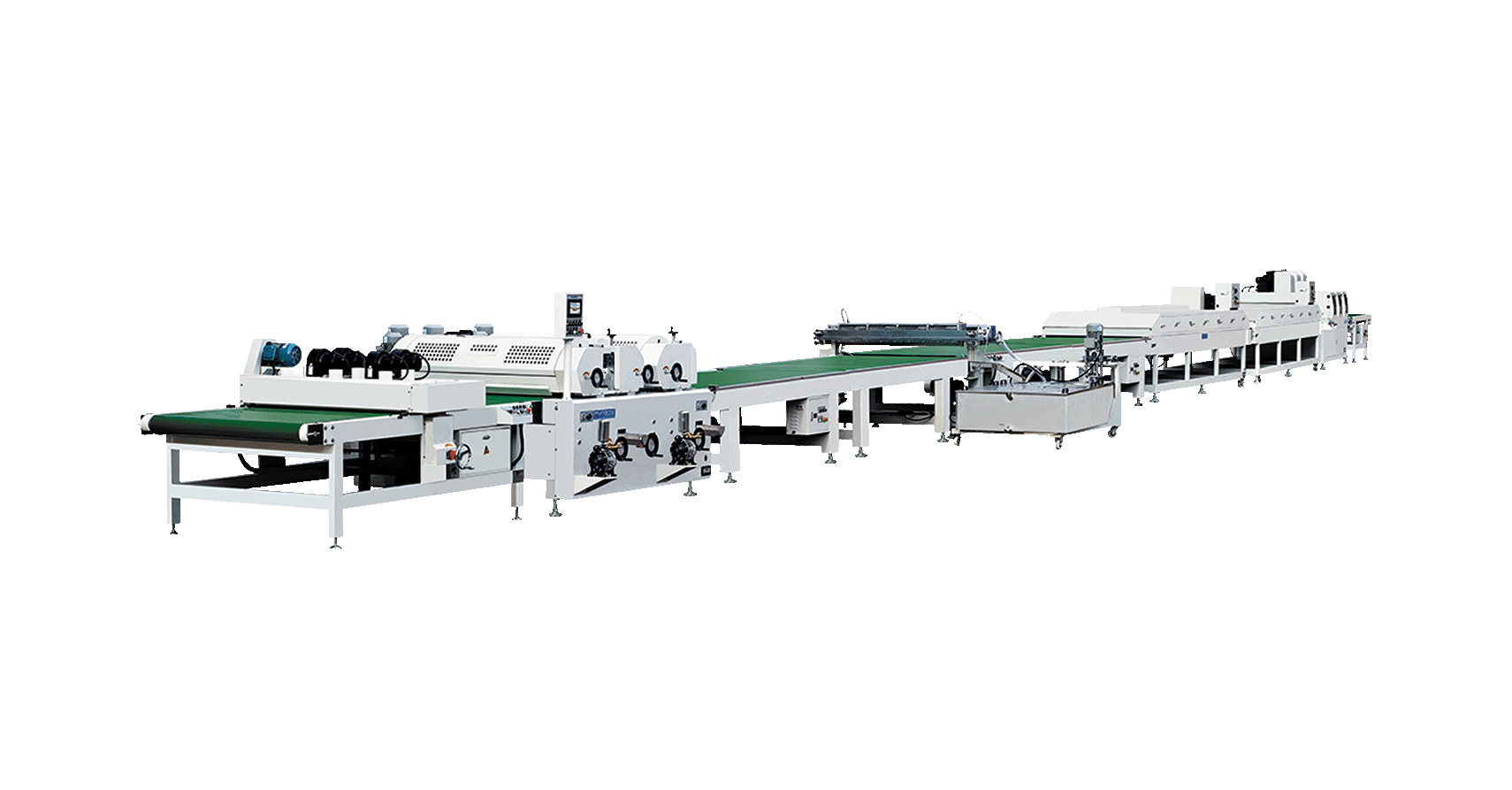


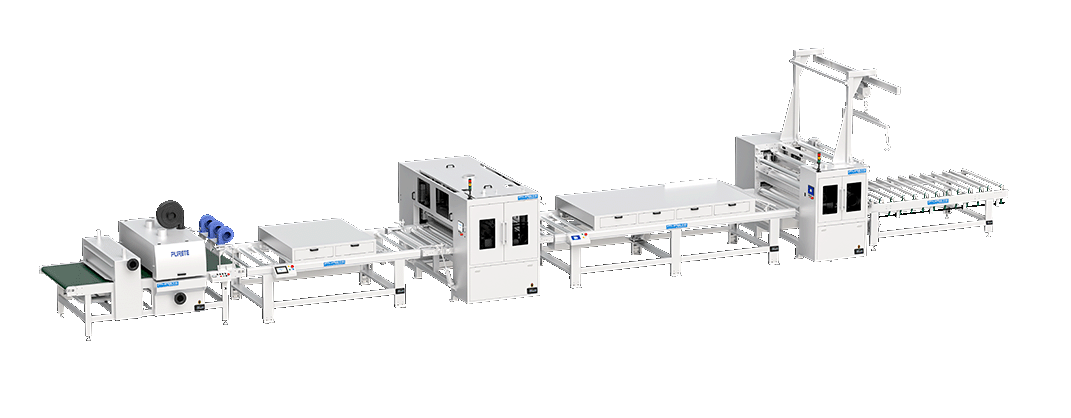
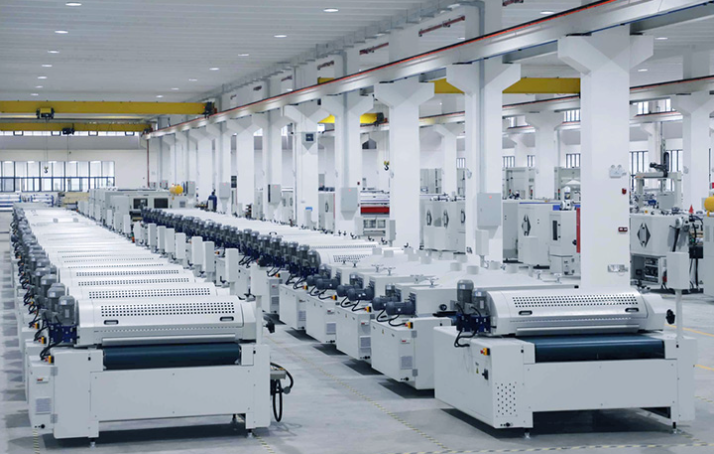
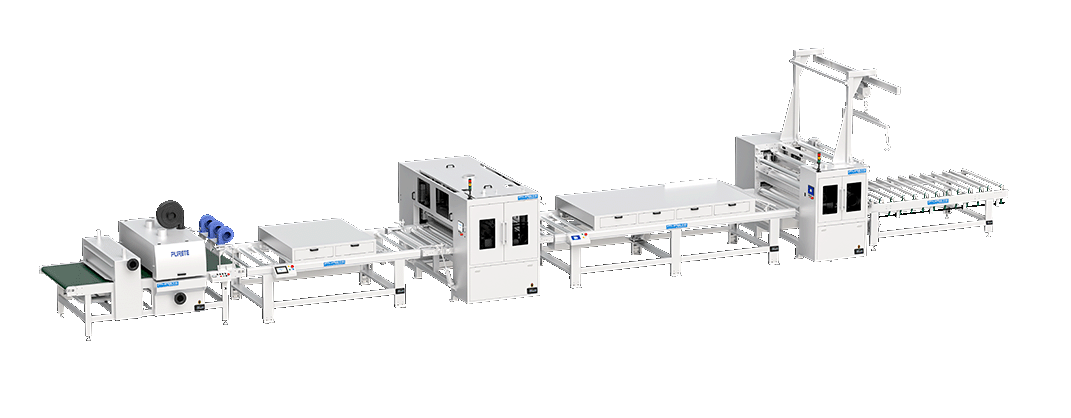
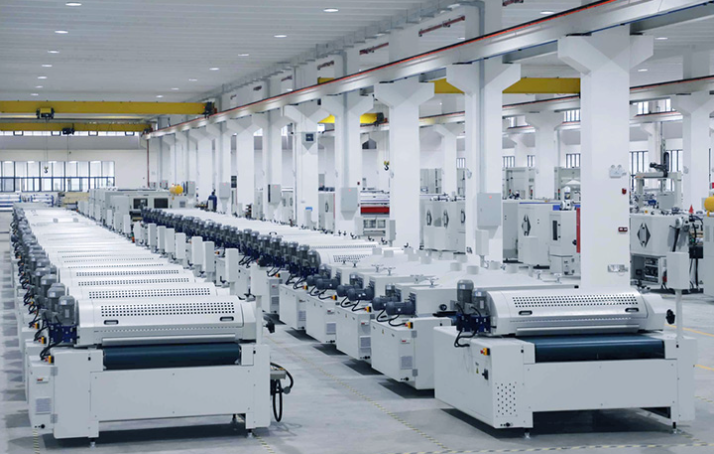
