Future Trends in Automatic Spray Painting Machine Systems


The automatic spray painting machine systems industry is continuously evolving, driven by technological advancements, increasing demand for efficiency, sustainability, and customization. As industries demand higher-quality finishes, faster production rates, and reduced environmental impact, the future of these systems is expected to be marked by innovation in automation, digitalization, and eco-friendly solutions. Below are the key trends that are shaping the future of automatic spray painting machine systems.
1. Integration of Industry 4.0 and IoT
· Smart Manufacturing: Industry 4.0 technologies, including the Internet of Things (IoT) and cloud computing, are set to revolutionize spray painting systems. These machines will become smarter, capable of real-time data analysis and remote monitoring, allowing operators to adjust parameters like spray flow, speed, and pressure from anywhere.
· Predictive Maintenance: Sensors and data analytics will predict equipment failures before they happen, minimizing downtime and reducing repair costs. This capability can significantly improve machine lifespan and reliability.
· Advanced Process Control: AI-powered systems will optimize spray painting processes, adjusting parameters on-the-fly based on real-time feedback, ensuring consistent finishes and minimizing waste.
2. Enhanced Automation with Robotics
· Robotic Spray Painting: Robotics are already a key part of modern spray painting systems, and their role will continue to grow. Advanced robotic arms with improved flexibility, precision, and speed will enable more complex and accurate coatings, especially in industries like automotive, aerospace, and electronics.
· Collaborative Robots (Cobots): Cobots, designed to work alongside human operators, will become more prevalent. These robots can handle repetitive and dangerous tasks while allowing humans to focus on more complex operations. Their ease of integration and flexibility make them ideal for dynamic production lines.
3. Eco-Friendly and Sustainable Technologies
· Water-Based Coatings: As regulations tighten on the use of volatile organic compounds (VOCs), the future will see a rise in water-based and low-VOC coatings. These coatings are safer for the environment and healthier for workers while still providing the durability and finish required in industrial applications.
· Powder Coating: Powder coating is a dry finishing process that has become increasingly popular due to its environmental benefits. It produces fewer pollutants, is more energy-efficient, and has a higher transfer efficiency compared to traditional liquid coatings.
· Recyclable and Biodegradable Paints: The development of eco-friendly, recyclable, and biodegradable paints is expected to grow, responding to both regulatory demands and consumer preferences for sustainable practices in manufacturing.
4. Artificial Intelligence and Machine Learning
· AI-Driven Optimization: The incorporation of artificial intelligence (AI) and machine learning (ML) algorithms will enable automatic spray painting systems to continuously learn from past applications and improve performance. AI will be able to detect imperfections in real-time, adjusting parameters for a flawless finish.
· Automated Quality Control: AI-powered cameras and sensors will assess the quality of the paint finish, identifying defects like runs, streaks, or uneven coverage, and automatically adjust the spray process to ensure perfection every time.
5. Increased Customization and Flexibility
· Customizable Spray Patterns: With more advanced programming and robotic arms, future spray painting systems will offer increased flexibility in spray patterns. Whether it's for intricate designs or large flat surfaces, operators will be able to program and modify the spray patterns to suit each unique application.
· Batch and Mass Customization: In industries like automotive or electronics, the demand for customization is on the rise. Future systems will allow for mass customization without sacrificing speed or quality, offering personalized designs and finishes for individual products while maintaining efficient production rates.
6. Digitalization and Software Integration
· Digital Twin Technology: The use of digital twins—virtual replicas of physical spray painting systems—will enable manufacturers to simulate the spray painting process in a virtual environment before executing it on the production floor. This technology allows for process optimization, error detection, and performance monitoring in real-time.
· Advanced Software Interfaces: Software will continue to improve, providing more intuitive, user-friendly interfaces that offer detailed insights into every stage of the spray painting process. These interfaces will also allow operators to track production metrics, manage inventory, and adjust system settings remotely.
7. Faster Drying and Curing Technologies
· UV-Curing Systems: UV-curable coatings are expected to become more prevalent, especially in industries that demand quick turnaround times. These coatings cure almost instantaneously under UV light, reducing drying time significantly and improving throughput.
· Infrared (IR) Drying: The use of infrared drying systems to speed up the drying process is set to increase. IR technology provides efficient heat transfer, speeding up the drying time without compromising the quality of the finish.
8. Adaptive Spray Technology
· Variable Flow and Pressure Control: Future spray painting machines will feature adaptive spray technology that adjusts flow rates and pressure in real time based on factors like surface texture, ambient temperature, and humidity. This will lead to a more consistent application, especially in challenging environments.
· Auto-adjusting Spray Guns: Spray guns equipped with advanced sensors will automatically adjust nozzle size, spray pattern, and pressure to optimize material usage and ensure consistent coverage across a range of surfaces and components.
9. Integration with Other Manufacturing Processes
· Seamless Integration with Assembly Lines: Future automatic spray painting systems will be more seamlessly integrated into overall manufacturing lines, allowing for continuous, uninterrupted production processes. These systems will be able to work with various stages of production, from pre-treatment to final assembly, reducing the need for manual intervention.
· End-to-End Automation: Entire production lines, including spray painting and packaging, will become fully automated. Automated spray painting machines will communicate with other machines in the production line, sharing data to streamline the workflow, reduce delays, and improve overall efficiency.
10. Greater Focus on Worker Health and Safety
· Zero Contact Spray Systems: To improve worker safety and reduce exposure to hazardous materials, zero-contact spray systems will be more widely implemented. These systems will use robotic arms and automated controls to handle all painting tasks, minimizing human interaction with chemicals and reducing health risks.
· Advanced Ventilation and Filtration: New spray booths will feature advanced ventilation systems, including better filtration to capture and remove harmful fumes, particles, and overspray from the air, ensuring safer environments for workers.
The future of automatic spray painting systems is one of increased sophistication, driven by innovations in AI, robotics, sustainability, and integration with Industry 4.0 technologies. These advancements will not only improve operational efficiency and quality but will also lead to more flexible, environmentally friendly, and customizable solutions for a wide range of industries. As the demand for faster, more precise, and greener manufacturing grows, automatic spray painting systems will continue to play a crucial role in shaping the future of industrial coatings.
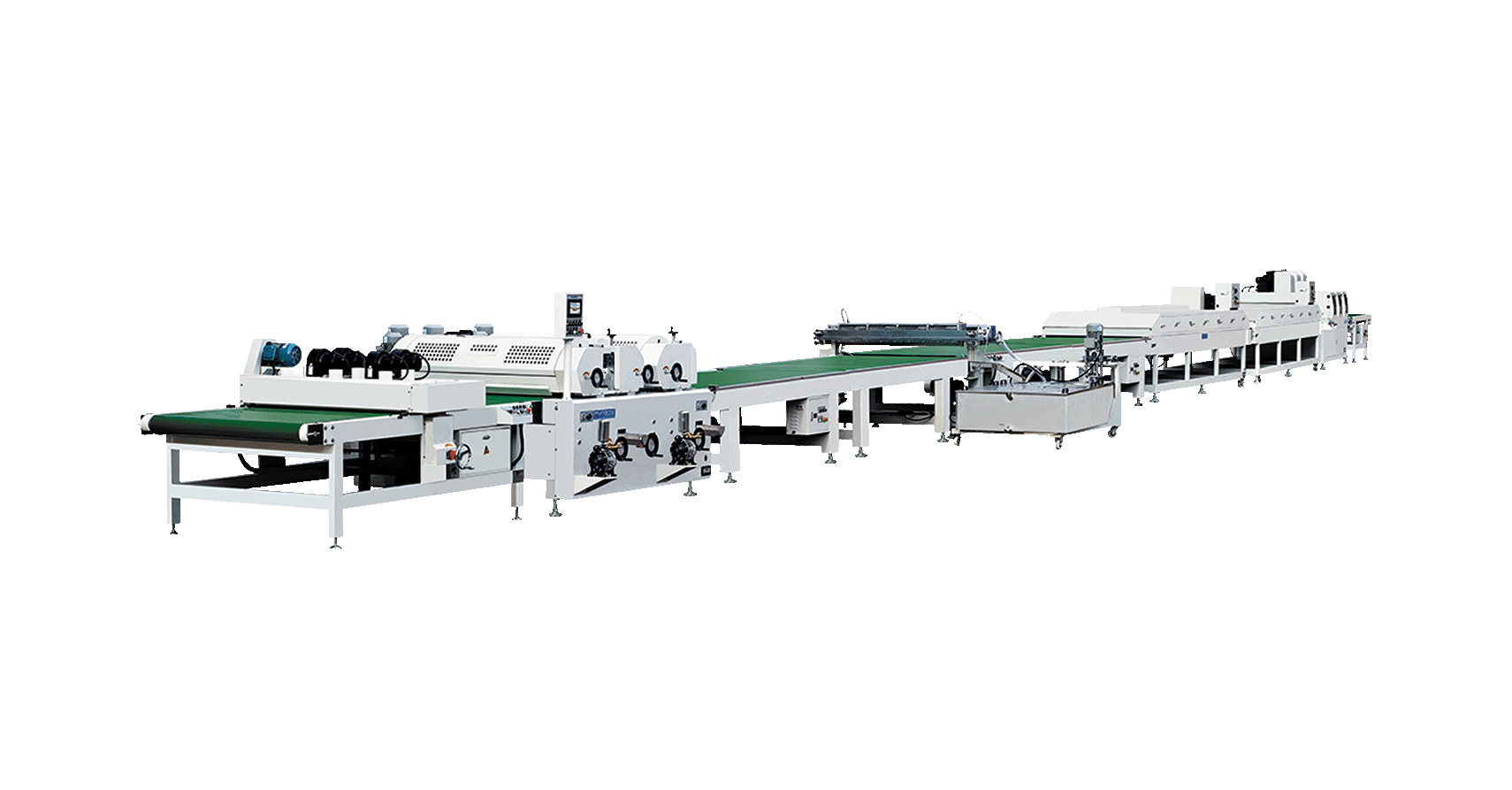


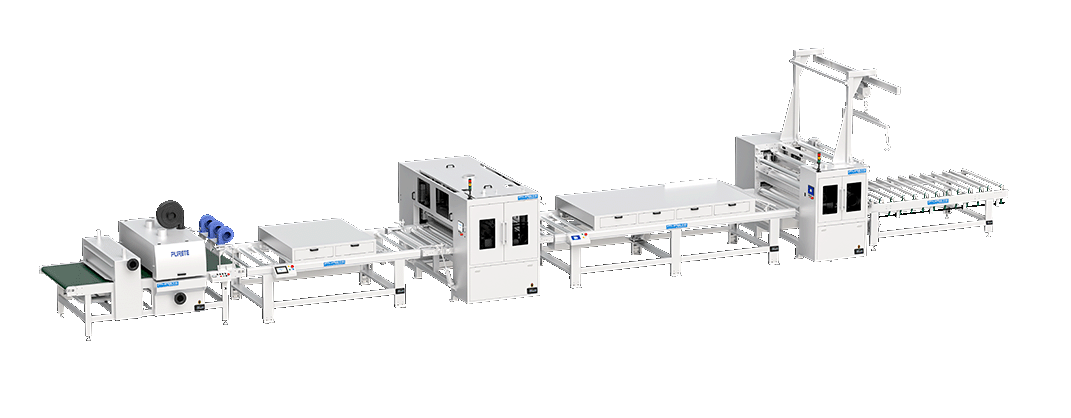
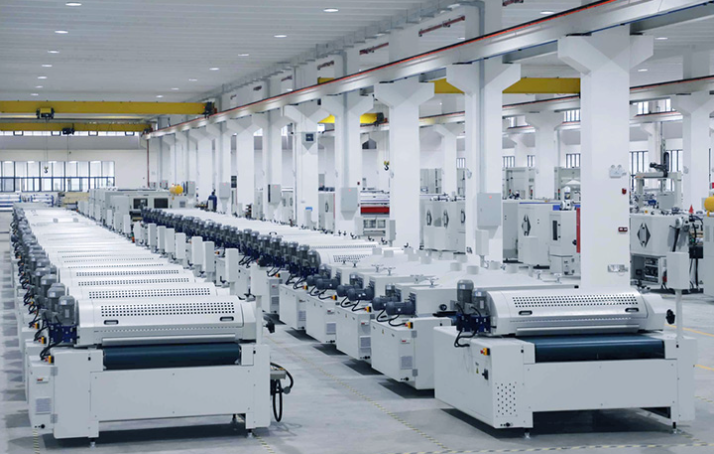
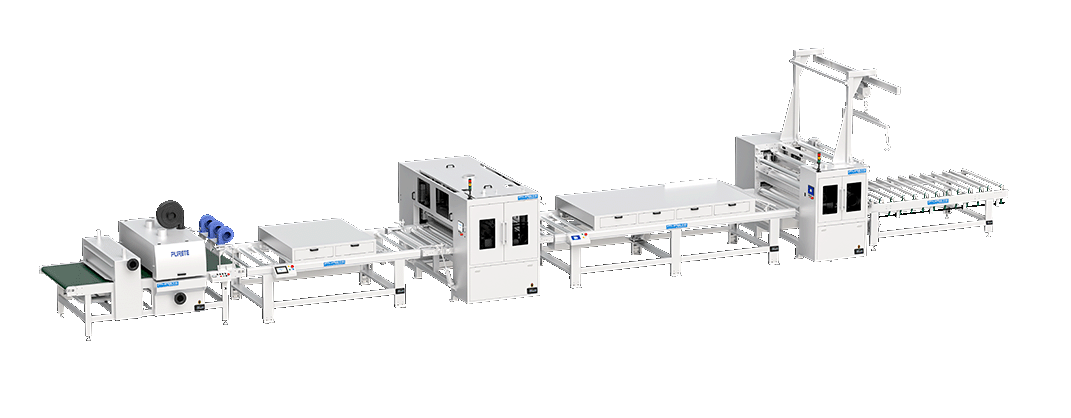
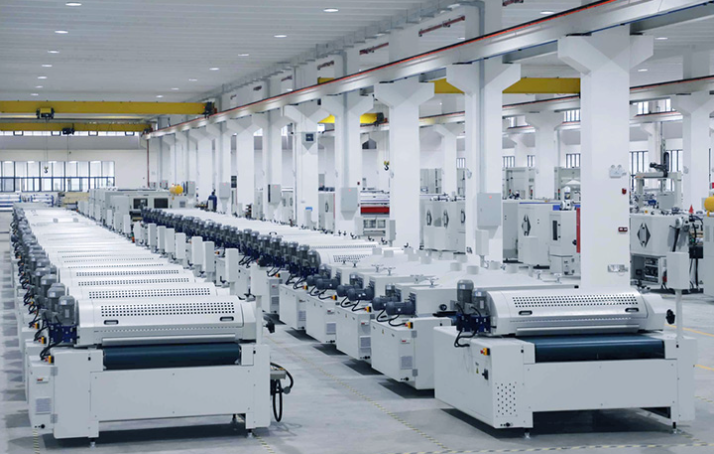
